In the dynamic world of manufacturing, Arden Dies Limited stands out as a pioneering force, growing from humble beginnings in a family cellar to becoming a globally recognised die-maker in the packaging sector. As a family-owned business now in its third generation, Arden has consistently embraced innovation and leadership, earning accolades such as the 2024 Manufacturing Family Business of the Year.
Angela Robinson, Manufacturing Advisor, sat down with Sarah Poynter, Operations Director, to discuss how Arden Dies has been empowering its team leaders with the tools and confidence to excel, and why investing in leadership is essential for long-term growth in the fast-evolving manufacturing industry.
Angela: Arden Dies has an incredible history, from starting in your family’s cellar to becoming world-renowned in the packaging industry for your quality die-cutting. Can you tell us more about the company’s journey?
Sarah: Absolutely! Arden Dies was founded by my grandfather and his brother in 1964 in Stockport. What started as a small family operation has grown into the Arden Group, which now includes a die-making division, an engraving arm, and a software company. We're in our third generation of family ownership and employ nearly 300 people worldwide.
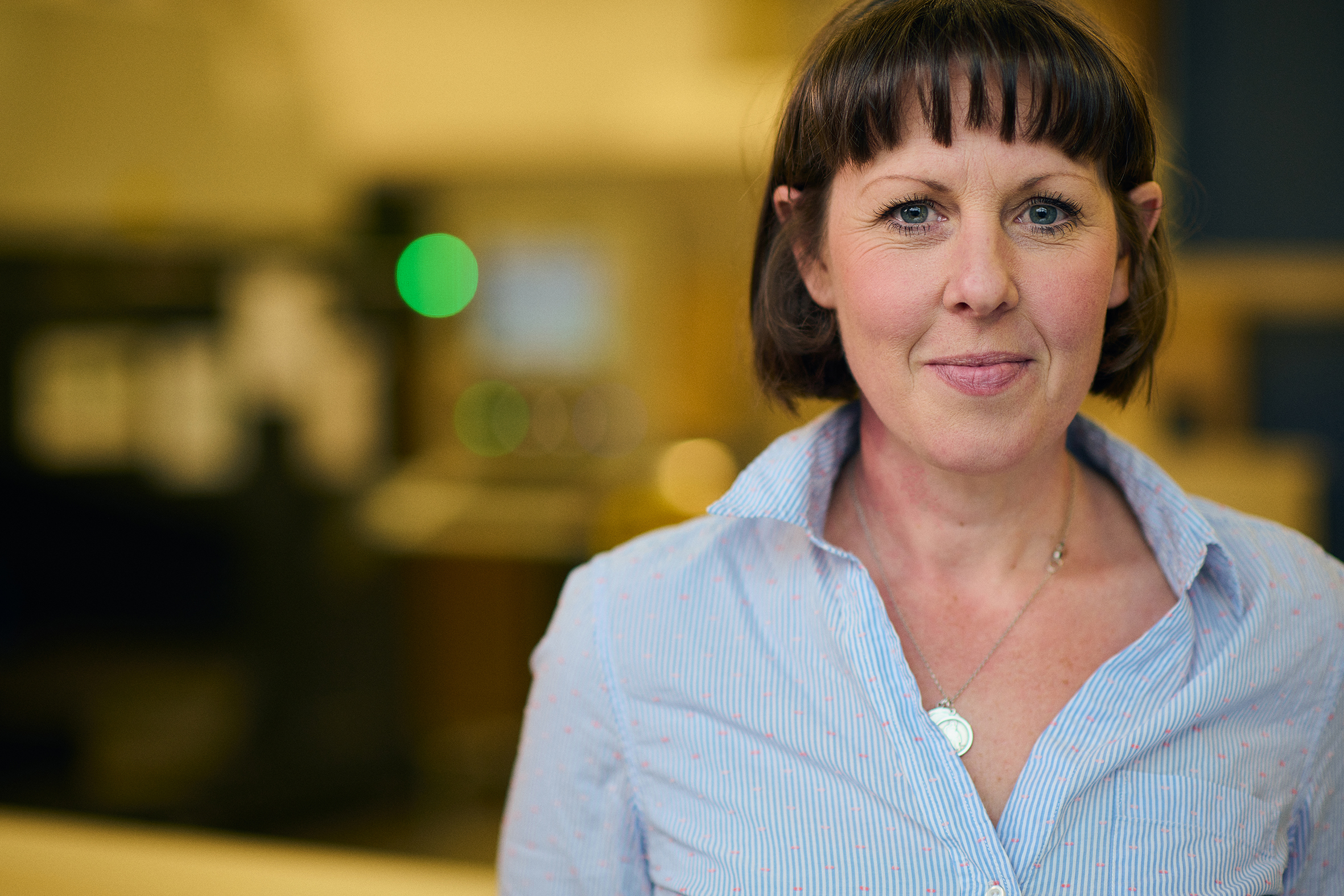
Angela: Arden has achieved tremendous success, especially with your recent awards. Could you share more about being crowned Manufacturing Family Business of the Year and Family Business of the Year for the North of England and Northern Ireland?
Sarah: Winning those awards was a proud moment for the whole family. The recognition from Family Business United highlighted the dedication, hard work, and innovation we’ve put into growing the business. It’s also a testament to our amazing team. We have always been committed to continuous improvement, and these awards reinforce the impact we’re making both locally and internationally.
Angela: That’s fantastic! As a world-renowned leader in die-making and packaging solutions, how do you continue to innovate and meet the evolving demands of the industry?
Sarah: Innovation is at the heart of everything we do. Whether it’s investing in the latest tooling technologies or developing our software for the packaging industry, we’re always looking to improve. We work closely with major blue-chip companies, and that pushes us to remain competitive. For instance, our die-making and tooling solutions are unmatched, and our Arden Software has revolutionised the CAD/CAM systems used in the industry.
Angela: I understand that leadership development is a key focus for you, especially when it comes to first-line management. Could you tell us about the challenges your team leaders have been facing?
Sarah: Yes, we have a group of team leaders who run very busy shifts, but they often struggle with some of the daily challenges that come with first-line management. We recognised that while they had the technical knowledge, there were opportunities to enhance their management skills – whether it’s communicating better, delegating tasks, or handling conflict. After discussing the situation with you, we decided that the Manufacturing Culture and Leadership Workshop would be incredibly valuable for them.
Angela: That’s right! Stephen Booth and I delivered the workshop on-site, and I must say, your team leaders were fantastic to work with. How did you feel the workshop went?
Sarah: It was incredibly effective! The workshop really pushed them out of their comfort zones and gave them practical tools to manage their teams more confidently. The activities were very hands-on, and they found the session on asking open questions particularly insightful. The feedback I received was overwhelmingly positive – everyone felt more confident and ready to apply what they’d learned immediately.
Angela: It was great to see such enthusiasm from your team. The goal of the workshop was to address challenges like managing difficult conversations, delegating tasks, and improving communication. Do you think it achieved that?
Sarah: Absolutely! The exercises around managing conflict and delegating tasks have already made a difference in their day-to-day management. One of the key takeaways for the team was how to handle difficult conversations confidently. We’ve already seen improvements in how they’re managing their shifts, which is a direct result of the training.
Angela: That’s brilliant to hear. It’s great to see that the workshop has had such a tangible impact. Moving forward, what are your priorities for leadership development at Arden?
Sarah: We want to continue investing in our leaders. The Manufacturing Culture and Leadership Workshop was just the beginning. We’re planning to build on this momentum by doing more training delivered by GM Business Growth Hub, particularly in problem-solving and lean manufacturing practices, to further enhance productivity and team cohesion.
Angela: It sounds like Arden is on an exciting path! Thank you, Sarah, for sharing your journey and your feedback about our workshop. It’s been a pleasure working with your team, and we look forward to continuing our collaboration.
If you’re interested in speaking to one of our specialist Manufacturing Advisors about improving your manufacturing operations, get in touch with us today!
Get in touch
Please contact us at 0161 3593050 or query below.
Take that first step and we’ll support you with whatever you need to succeed.
Sign-up to our newsletter
Insights, news, events and opportunities straight to your inbox.