In our latest interview, we had the pleasure of speaking with Tom Haworth, a Manufacturing Business Advisor at GM Business Growth Hub. Tom has a wealth of experience across multiple sectors and countries, which gives him a unique perspective on the manufacturing industry. A constant pursuit of efficiency and innovation marks his journey.
Career Journey
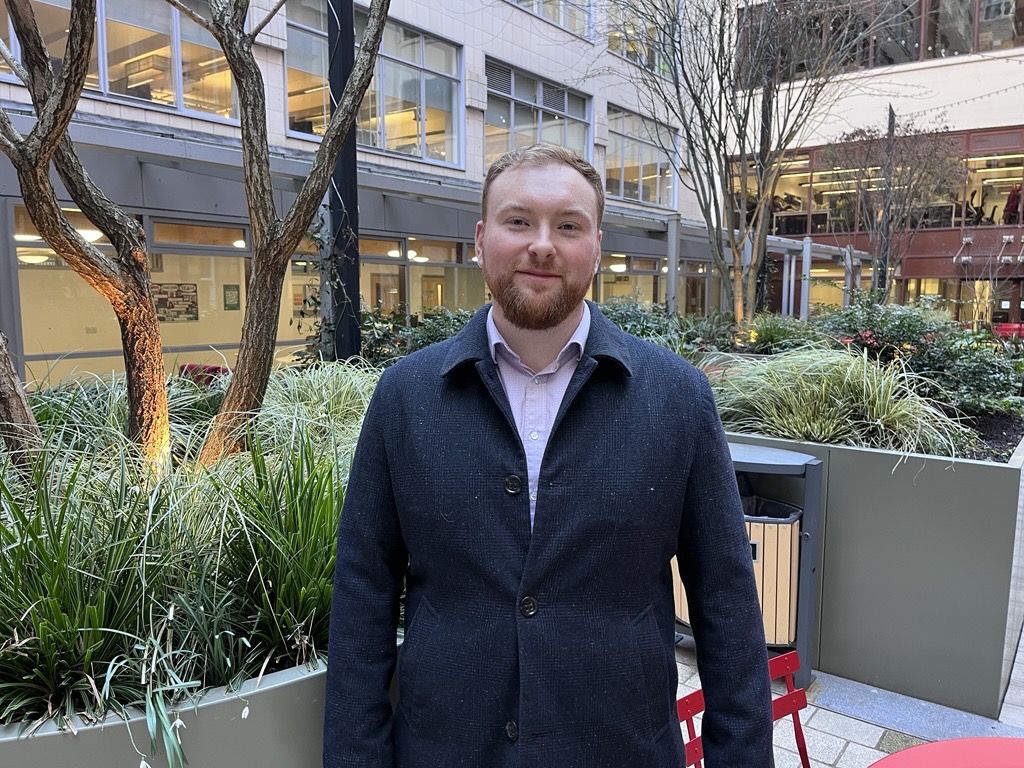
Q: Hi Tom, welcome to the team! Could you introduce yourself and share a little about your background in manufacturing?
Over the past six to seven years, I have primarily worked in food manufacturing across the UK. Before that, I managed smaller businesses in various sectors, including tech, merchandising, and gifts. My experience spans over 20 countries, and I have been involved in a wide variety of factory settings. This breadth of exposure has given me a well-rounded view of both manufacturing and business operations.
While running my own ventures, I was particularly focused on product development and innovation. In the food manufacturing sector, I focused on establishing production processes, setting quality standards, and conducting risk assessments. One standout moment was overseeing a turkey production line during the busy Christmas season – which was a baptism of fire into food manufacturing.
In my continuous improvement (CI) role, I led multiple projects that resulted in annual savings of seven figures. This included conducting time and motion studies, optimising workflows, and standardising key processes. By mentoring and training teams, we achieved significant efficiency gains, contributing a double-digit percentage increment to the company's bottom line. One notable success involved reducing drip loss during chicken basting through detailed process analysis.
Q: You also helped set up a new factory for a food manufacturer. Tell us more about that project.
Setting up a brand-new, £30 million, state-of-the-art factory was a major milestone. My role was to ensure that the facility was both efficient and safe. This meant everything from selecting the right equipment and designing the layout to training staff and building standard operating procedures.
We had to stress-test the machinery to guarantee it could meet output targets while also making sure operators were fully trained. The factory setup included a comprehensive approach, from choosing the right equipment to ensuring that health and safety standards were fully met. It was a collaborative effort involving specialists at every stage.
Overcoming Challenges
Q: What challenges have you faced in manufacturing, and how did you tackle them?
One of the biggest challenges in management is ensuring that staff members are engaged and motivated. It’s crucial to take the time to get to know the team and involve them in the decision-making process. Another significant challenge is streamlining production processes to reduce waste and enhance efficiency. This involves detailed analysis and ongoing improvement efforts. In food manufacturing, issues like drip loss and inconsistent equipment performance demanded creative thinking and close work with suppliers to find the right fix.
Q: What would you say is the most important thing for manufacturers to manage during tough times and to boost efficiency?
The first step is to listen to the people on the shop floor. Understanding their needs and challenges is vital – they usually know where the real issues are. Financial vigilance is also critical – make sure your pricing is right, and your overheads are under control. Balancing multiple projects while coaching teams and analysing financial data is essential.
For instance, when setting up production lines, it’s not just about the machinery – it’s about whether your team can operate it consistently and safely. That’s where training and process design come into play.
From Factory Floor to Business Advisor
Q: Why did you choose to move into a business advisor role, and how does your past experience shape your approach?
I have a genuine passion for helping businesses succeed and thrive. I enjoy the challenge of finding solutions to complex problems. My international and cross-sector experience means I can draw on a wide range of ideas and apply them in new contexts. As a business advisor, I combine a people-first mindset with a strong grasp of numbers and a commitment to continuous improvement. My goal is to help manufacturers achieve their goals and navigate change with confidence.
Q: Do you have any advice for manufacturers navigating the current economic climate?
Keep a close eye on your numbers and understand your market inside out. Be flexible and responsive to changes. Don’t hesitate to seek support – the GM Business Growth Hub has a lot to offer. Focus on making great products efficiently and be ready to adapt. With rising costs and market uncertainty, cash flow management and agility are more important than ever.
Tom’s insights reflect his deep knowledge of the manufacturing landscape and his commitment to helping businesses thrive. His people-centric approach, financial acumen, and adaptability make him a valuable advisor for any manufacturing business looking to improve efficiency and achieve continuous improvement.
Would you like tailored support to improve your processes, efficiency, and bottom line? Connect with one of our expert Manufacturing Advisors today.
Get in touch
Please contact us at 0161 3593050 or query below.
Take that first step and we’ll support you with whatever you need to succeed.
Sign-up to our newsletter
Insights, news, events and opportunities straight to your inbox.