We recently caught up with Stuart Hope, a seasoned manufacturing professional with over 20 years of experience, who has now joined the GM Business Growth Hub as a manufacturing advisor. Stuart’s extensive background in operations management, logistics and supply chain, gives him a unique perspective on the challenges manufacturers face today. His passion for continuous improvement and dedication to optimising efficiency makes him a valuable asset to our team and a key resource for manufacturers in Greater Manchester.
Hi Stuart, welcome to the team! Could you share a bit about your career journey and what brought you to this new role?
Thanks, it’s exciting to be here! I started my career in the 1990s, initially working in logistics. In 2000, I transitioned into a leadership role, and over the years, I’ve worked in various areas of manufacturing—operations, production management, and supply chain management. This experience, across both large and small companies, gave me a solid understanding of the entire operational cycle, from receiving orders to delivering the finished product.
For the past two decades, my focus has been on optimising processes and minimising waste, using methods like 5S and lean manufacturing. Joining GM Business Growth Hub as a business advisor felt like a natural next step—now, I can use what I’ve learned to help manufacturers in Greater Manchester improve their operations and become more competitive.
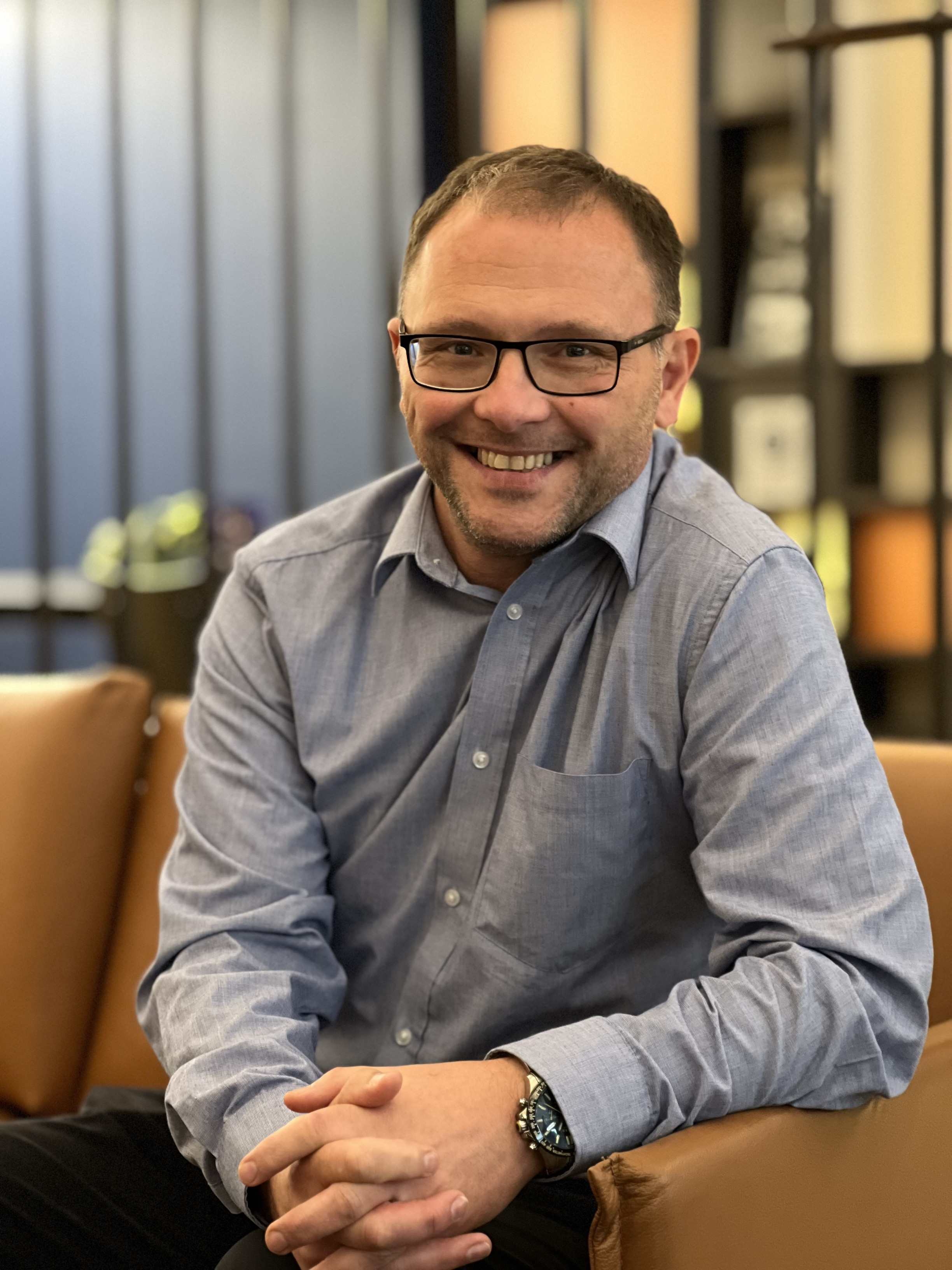
That’s quite the range of experience! Can you share an example of a time when you helped a company improve its operational efficiency?
One of the standout examples is from my time worked with a Stockport-based manufacturer. The company had multiple factories, each responsible for different parts of the production process, which meant goods had to be transported between sites during manufacturing. This added unnecessary cost and extended lead times, which hurt the company’s competitiveness.
Working alongside the operations director, we reviewed the entire production cycle and decided to centralise the embroidery process by relocating machines from Lancashire to Stockport. We also introduced a new machines to the factory. This change not only required the physical move of equipment but also a complete reorganisation of the factory layout and workflows.
By centralising the production processes, we reduced the lead time from 18 days to less than 10 days – a 50% increase in efficiency. Additionally, we cut down on transportation costs and reduced waste, which made a real difference to the business and contributed to enhancing the company’s competitiveness.
That is a significant improvement! What were some of the key challenges in making that change?
The biggest challenge wasn’t moving the equipment – it was changing how people worked. Manufacturing is often seen as a repetitive process, and many people are resistant to change, especially when the current system seems to be working. You hear things like, “Don’t fix it if it is not broken”, or “There is no need to reinvent the wheel” but that mindset can hold businesses back.
The key is to recognise that continuous improvement is an ongoing journey, not a one-off project. You have to break down changes into manageable steps and allow people time to adjust. Once they see the benefits of those small changes – like reduced lead times or less waste – they’re more open to embracing further improvements.
It sounds like building a culture of continuous improvement is key. What advice would you give to manufacturers looking to start that journey?
Creating a culture of continuous improvement is vital but it doesn’t happen overnight. It’s the result of making many small changes over time. My advice would be to start small. Don’t try to overhaul everything at once. Focus on one area, make improvements, and let people see the results. Once the team buys into the process, you can gradually expand that mindset across the whole operation. That’s when you can really build a culture where everyone is looking for ways to make the business better.
And of course, if you’re unsure where to start, the GM Business Growth Hub is here to help. We can provide tailored support to identify areas for improvement and guide you through the steps to make your operations more efficient and sustainable.
If you're ready to begin your own journey toward continuous improvement, leave your details below, and one of our manufacturing advisors will be in touch to discuss how we can help streamline your operations, reduce waste, and boost efficiency.
Get in touch
Please contact us at 0161 3593050 or query below.
Take that first step and we’ll support you with whatever you need to succeed.
Sign-up to our newsletter
Insights, news, events and opportunities straight to your inbox.