In the fast-paced world of manufacturing, efficiency is everything. One of the most common questions we receive from our manufacturing clients is, "What’s the quickest way to increase productivity in a factory?" Our answer consistently points to a proven Lean principle – the Gemba Walk. It stands as a foundational practice in Lean Manufacturing that can significantly improve productivity and workplace culture when done right.
But what exactly is a Gemba Walk?
Gemba is a Japanese word meaning "the real place" or "where the action happens." The practice was developed by Taiichi Ohno, a Toyota executive and the father of the Just-in-time (JIT) production system. In manufacturing, Gemba translates to the factory floor – the heart of production. A Gemba Walk refers to management spending time on the shop floor, it is not just about “walking around”– it’s a structured approach designed to bring tangible benefits to the workplace.
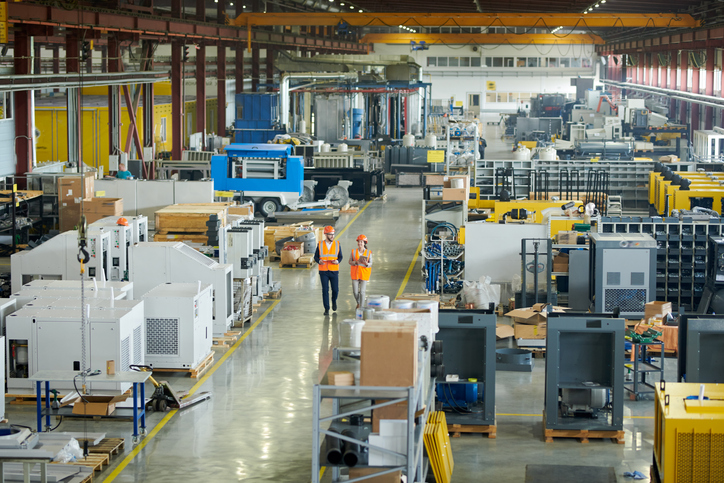
Why walk the factory floor?
The key to understanding any workplace is direct observation. The Gemba Walk allows managers and leaders to see what’s happening in real-time, catch inefficiencies, and get valuable insights from those who know the processes best – the employees. From spotting potential safety hazards to reviewing machine conditions, this hands-on approach provides an opportunity to identify waste and opportunities for continuous improvement.
The power of observing, engaging, and improving
The underlying principles of the Gemba Walk are simple but effective: Observe, Engage, and Improve.
Observation: The first step is understanding the factory’s day-to-day reality. This involves watching without preconceived notions. Employees don’t need to know you’re observing a specific plan – they should continue with their usual routine. Over time, you’ll authenticate your findings to form a clear picture of what’s happening.
Engagement: Gemba is more than just watching. It’s about building relationships with your employees. Ask questions, listen, and take notes. The people on the floor understand the good and bad points of their jobs better than anyone else. Engaging with them can offer insights into inefficiencies that may not be immediately apparent.
Improvement: Armed with the knowledge gathered during the Gemba Walk, it’s time to make improvements. Focus on known problem areas, but be sure to vary the walks to gain a holistic understanding of the factory. Importantly, work with your team to develop solutions – when employees are part of the process, embedding change becomes much easier.
How to prepare for your Gemba Walk
Effective Gemba Walks require preparation. Plan each walk in advance, allocating 30 minutes to an hour for each visit. Directors should aim to walk the floor once a week, while team leaders should do it daily. The insights gathered should be shared with the team and used for strategic decision-making and continuous improvement.
Sample checklist for your Gemba Walk:
- Is the workspace safe?
- Is the 5S system being followed?
- Are KPIs and performance measures accessible and up to date?
- Are standard operating procedures (SOPs) clear, up to date and visible?
- Is work on schedule, or falling behind?
- Are machines maintained and in good condition?
- Are tools standardised and stored properly when not in use?
- Are there any bottlenecks?
- Are there risks to work-in-progress items?
- Are there any leaks, spills, damage or abnormal noises?
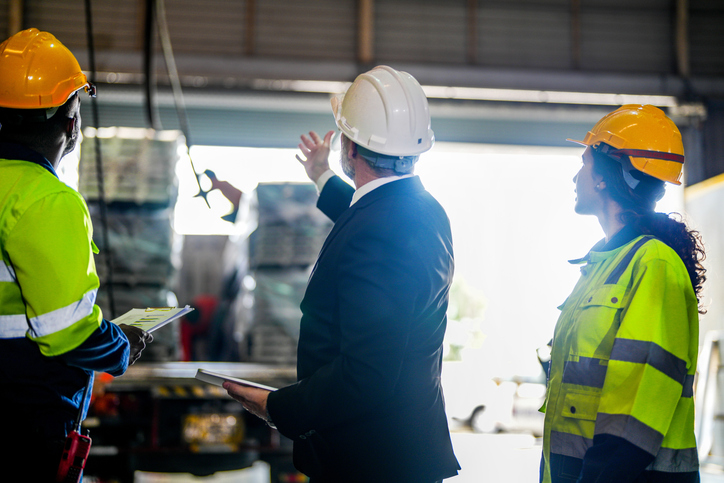
The answers to these questions will help you pinpoint inefficiencies and areas for improvement.
Avoid common pitfalls
While Gemba Walks are simple, they’re not without challenges. It’s important to stay calm when encountering inefficiencies, avoid undermining line managers, and refrain from making snap judgments. Above all, be mindful of the "observer effect" – if employees know they are being watched, they may adjust their behaviour. A well-executed Gemba Walk should provide a true reflection of daily operations without disrupting the flow of work.
It’s also important not to confuse Gemba with Management by Walking Around (MBWA), a less effective practice. As the management expert W. Edwards Deming pointed out, MBWA often fails because managers don’t pause long enough in any one spot to get meaningful insights. Gemba, by contrast, is about spending intentional time observing and engaging with specific processes.
The role of the GM Business Growth Hub in supporting manufacturers
The Gemba Walk is a powerful, yet simple tool that any manufacturing leader can use to improve productivity and foster a culture of continuous improvement. At GM Business Growth Hub, we encourage manufacturers to embrace Lean principles like the Gemba Walk to unlock new levels of operational efficiency. Our team of expert Manufacturing advisors is here to guide you to embed these practices into your day-to-day operations – whether through workshops, direct advisory support, or practical on-site assistance. If you're new to the Gemba Walk, we can even walk the factory floor with you to show you how it's done. Get in touch with our team today!
Get in touch
Please contact us at 0161 3593050 or query below.
Take that first step and we’ll support you with whatever you need to succeed.
Sign-up to our newsletter
Insights, news, events and opportunities straight to your inbox.